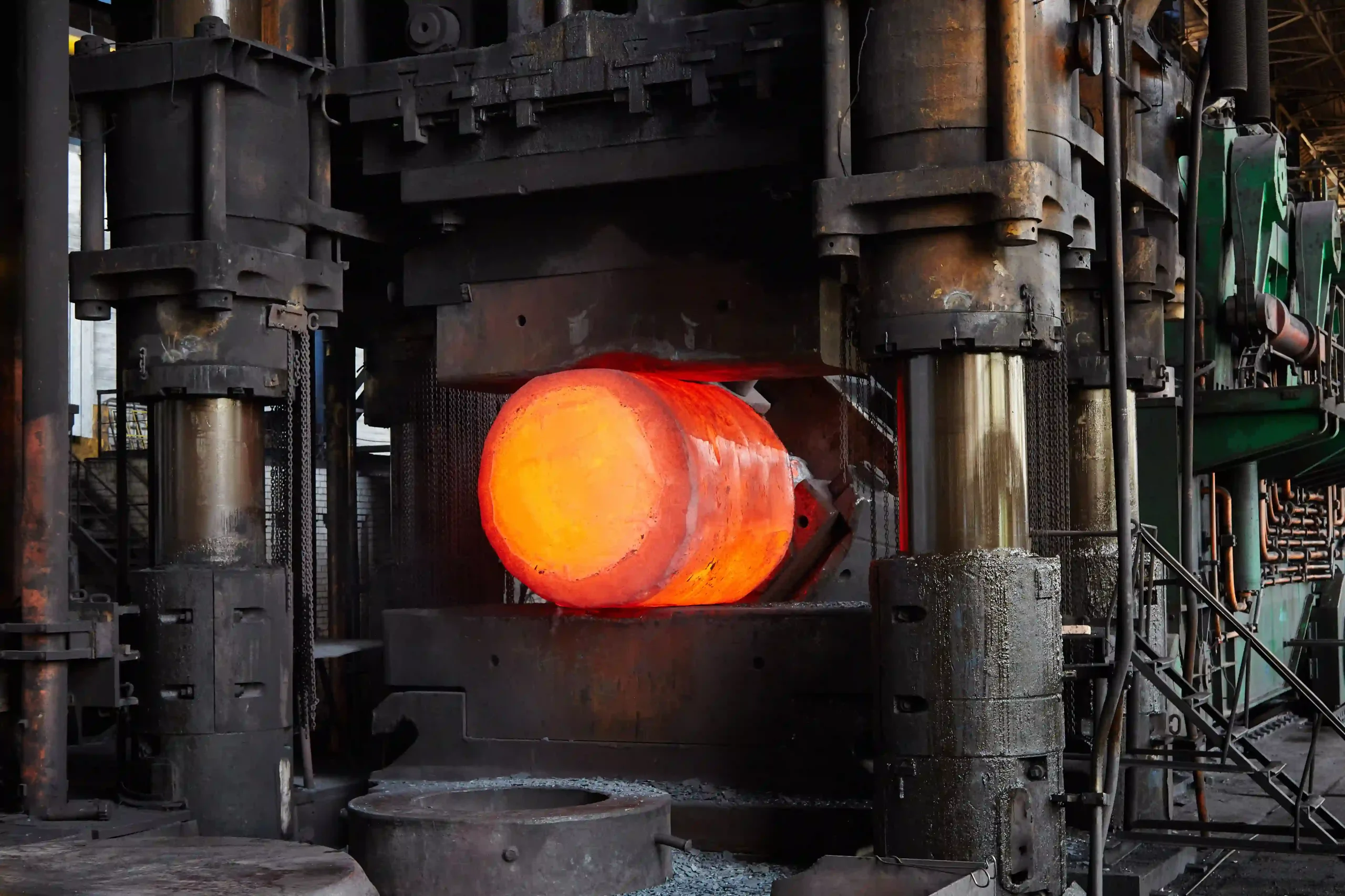
forging چیست؟
ساخت لوله به صورت forging، از طریق یک فرآیند دقیق به نام “forge”ساخته میشوند که شامل شکل دهی و فشرده سازی فلز گرم شده به شکل مورد نظر است. این روش منجر به تولید محصولاتی بسیار قوی و بادوام میشود که قادر به تحمل فشار بالا و دما های شدید هستند. در زیر توضیح کاملی از مراحل مختلف فرآیند تولید اتصالات لوله فورج شده آمده است.
انتخاب مواد اولیه مناسب
Forging، با انتخاب مواد اولیه مناسب آغاز میشود. معمولاً آلیاژ های فلزی با کیفیت بالا مانند فولاد کربنی، فولاد ضد زنگ، یا آلیاژ های نیکل بسته به کاربرد و ویژگی های مورد نیاز استفاده میشوند. این فرآیند انتخاب بسیار مهم است زیرا استحکام، دوام و عملکرد محصول نهایی را تعیین میکند. تولید کنندگان این مواد را از تأمین کنندگان معتبر تهیه کرده یا در داخل شرکت تولید میکنند تا کیفیت ثابت را تضمین کنند.
گرم کردن فلز در forging
پس از انتخاب مواد اولیه، فلز برای رسیدن به حالت قابل انعطاف گرم میشود. این مرحله فلز را نرم میکند و شکل دادن به آن را بدون ترک خوردگی ممکن میسازد. دمای مورد نیاز برای گرم کردن به نوع ماده مورد استفاده بستگی دارد. به عنوان مثال، فولاد ضد زنگ و فولاد کربنی به محدوده دمایی مختلفی نیاز دارند. فرآیند گرم کردن با استفاده از تجهیزات پیشرفته مانند کورهها یا ماشینهای گرمایش القایی انجام میشود تا توزیع یکنواخت گرما و کارایی تضمین شود.
شکل دهی به فلز در forging
فلز گرم شده سپس در یک پرس فورج قرار میگیرد و تحت فشار بالا به شکل دلخواه در میآید. فرآیند forge شامل استفاده از قالب ها و ابزار های تخصصی برای فشرده سازی و قالب گیری فلز است. پرس های forge، میتوانند هیدرولیکی، مکانیکی یا نیوماتیکی باشند که بسته به اندازه و پیچیدگی محصول انتخاب میشوند. این مرحله برای افزایش یکپارچگی ساختاری و ویژگیهای مکانیکی اتصالات لوله ضروری است و تضمین میکند که نیازهای سختگیرانه کاربردهای صنعتی را برآورده میکند.
برش مواد اضافی
پس از forging، محصول معمولاً دارای مواد اضافی در اطراف لبهها است که به آن «فلاش» میگویند. این مواد اضافی برای ایجاد یک محصول نهایی تمیز و کامل برش داده میشوند. فرآیند برش با استفاده از ابزارهایی مانند اره، سنگساب یا قیچی انجام میشود که بسته به اندازه و پیچیدگی اتصالات فورج شده متفاوت است. برش دقیق تضمین میکند که محصول الزامات ابعادی و زیبایی شناختی را برآورده میکند.
ماشین کاری برای دقت forging
اگر کاربرد به اشکال یا ویژگیهای خاصی نیاز داشته باشد، اتصالات forging، تحت فرآیند ماشین کاری اضافی قرار میگیرند. تجهیزات پیشرفته ای مانند تراش، فرز و ماشینهای حفاری برای دستیابی به مشخصات مورد نیاز استفاده میشوند. این مرحله برای ایجاد رزوه ها، جوش های سوکتی یا سایر ویژگیهای دقیق که برای عملکرد صحیح اتصالات در یک سیستم لوله کشی ضروری است، بسیار مهم است.
بازرسی کیفیت
مرحله نهایی در فرآیند تولید به صورت forging، بازرسی دقیق کیفیت است. این اطمینان میدهد که اتصالات تولید شده با استانداردهای صنعتی مطابقت داشته و مشخصات مشتری را برآورده میکنند. ابزارهای مختلفی از جمله کولیس، میکرومتر و تجهیزات تست اولتراسونیک برای بررسی ابعاد، کیفیت سطح و یکپارچگی داخلی استفاده میشود. بازرسی برای تضمین قابلیت اطمینان و ایمنی اتصالات فورج شده در کاربردهای واقعی ضروری است.
استاندارد ها و درجه بندی فشار در اتصالات
اتصالات لوله فورج شده مطابق با استانداردهای سختگیرانه صنعتی مانند:
- ASME/ANSI B16.11
- ASTM A105
- MSS SP-83
این استاندارد ها ابعاد، ویژگی های مواد و درجه بندی فشار اتصالات فورج شده را مشخص میکنند. محدوده اندازه معمولی اتصالات forge شده بین 1/8 اینچ تا 4 اینچ است و درجهبندی فشار تا 6000 PSI میرسد. با این حال، برخی تولیدکنندگان اندازههای بزرگ تر و درجهبندیه ای فشار بالاتر را برای برآورده کردن نیازهای خاص ارائه میدهند.
روش های forging: Open-Die and Closed-Die Forging
فرآیند فورجینگ را میتوان به دو روش اصلی تقسیم کرد: فورج قالب باز و فورج قالب بسته.
فورج قالب باز
که به نام فورج دستی نیز شناخته میشود، شامل ضربات مکرر چکش بر روی فلز برای تغییر شکل آن تا رسیدن به فرم مورد نظر است. فلز به طور کامل توسط قالب احاطه نمیشود و شکلدهی آن به مهارت اپراتور بستگی دارد. فورج قالب باز معمولاً برای تولید اشکال بزرگ و ساده، مانند قطعات مورد استفاده در صنایع هوافضا و نفت و گاز، استفاده میشود.
فورج قالب بسته
در این روش، فلز بین دو قالب پیشماشینکاری شده قرار میگیرد و تحت فشار بالا با استفاده از یک پرس هیدرولیک شکل داده میشود. قالبها طرحی از شکل مورد نظر را ایجاد میکنند که با اعمال فشار به فلز، نتیجهای دقیق و پیچیده به دست میآید. فورج قالب بسته سریعتر و مناسبتر برای قطعات کوچکتر و پیچیدهتر، مانند قطعات خودرویی و پزشکی است.
تفاوت اصلی بین این روشها در میزان کنترل بر شکل نهایی محصول است. فورج قالب باز به مهارت اپراتور متکی است، در حالی که فورج قالب بسته نتیجهای دقیق و قابل تکرار ارائه میدهد. هر روش مزایای منحصربهفردی بسته به کاربرد دارد.
کاربردها و مزایای لوله فورج شده
لوله فورج شده، در صنایعی مانند نفت و گاز، پتروشیمی و تولید برق ضروری هستند. توانایی آنها در تحمل فشار های بالا و دماهای شدید آن ها را برای کاربرد های حیاتی ایده آل میکند. انتخاب نوع اتصالات، مواد و روش forge بستگی به نیازهای خاص سیستم پایپینگ دارد. در ادامه به بررسی بیشتر کاربرد و مزایای forging پرداخته ایم:
کاربرد forging pipe
اتصالات لوله فورج شده به دلیل استحکام و قابلیت اطمینان بالا، در صنایع مهمی مانند نفت و گاز، پتروشیمی و تولید برق به کار گرفته میشوند. این اتصالات در سیستمهای انتقال سیال، خطوط لوله فشار قوی، و تأسیسات صنعتی استفاده میشوند، جایی که مقاومت در برابر فشارهای بالا و شرایط محیطی سخت ضروری است. در صنایع نفت و گاز، اتصالات فورج شده برای انتقال ایمن مواد شیمیایی خورنده، گازهای فشرده و سیالات داغ به کار میروند. در صنایع پتروشیمی و تولید برق نیز این اتصالات برای مدیریت جریان سیالات و بخارات تحت فشار بالا نقش حیاتی ایفا میکنند. توانایی این اتصالات در حفظ یکپارچگی ساختاری تحت شرایط دشوار، آنها را به انتخابی ایدهآل برای کاربردهای حساس تبدیل کرده است.
مزایای forging pipe
لوله های فورج شده، مزایای متعددی دارند که آنها را از سایر گزینههای موجود متمایز میکند. این مدل ها به دلیل فرآیند تولید خاص خود، از ساختاری فشرده و یکنواخت برخوردارند که مقاومت بالایی در برابر ترک خوردگی، فشار های داخلی و تغییرات دما فراهم میکند. دوام بالای آنها، عمر طولانی تری نسبت به لوله های جوشی، یا ریختهگری شده ارائه میدهد، که هزینه های نگهداری و تعمیرات را کاهش میدهد. علاوه بر این، لوله فورج شده، میتواند با استفاده از مواد مختلف مانند فولاد کربنی، فولاد ضد زنگ یا آلیاژهای نیکل تولید شوند که امکان تطبیق با نیازهای متنوع سیستم پایپینگ را فراهم میکند. این ویژگی ها، همراه با توانایی سفارشی سازی آنها برای تحمل شرایط خاص، برای پروژه های صنعتی و زیرساختی حیاتی ایدهآل میکند.
تیم فنی و مهندسی فولاد تبار در تقاطع تخصص و دقت در تلاش است راه حل های بی نظیری را در سیستم های تجاری، مهندسی و صنعتی ارائه دهد. ما در مجموعه فولاد تبار، به دنبال آموزش مطالب علمی در زمینه piping material هستیم تا بتوانیم باعث افزایش مهارت های فنی و مهندسی شما باشیم تعهد ما شما را به اهداف عملیاتی خود تضمین می نماید.
با ما همراه شوید تا عملکرد مهندسی خود را با راه حل های نوآورانه و قابل اعتماد ارتقا دهید
دیدگاهتان را بنویسید