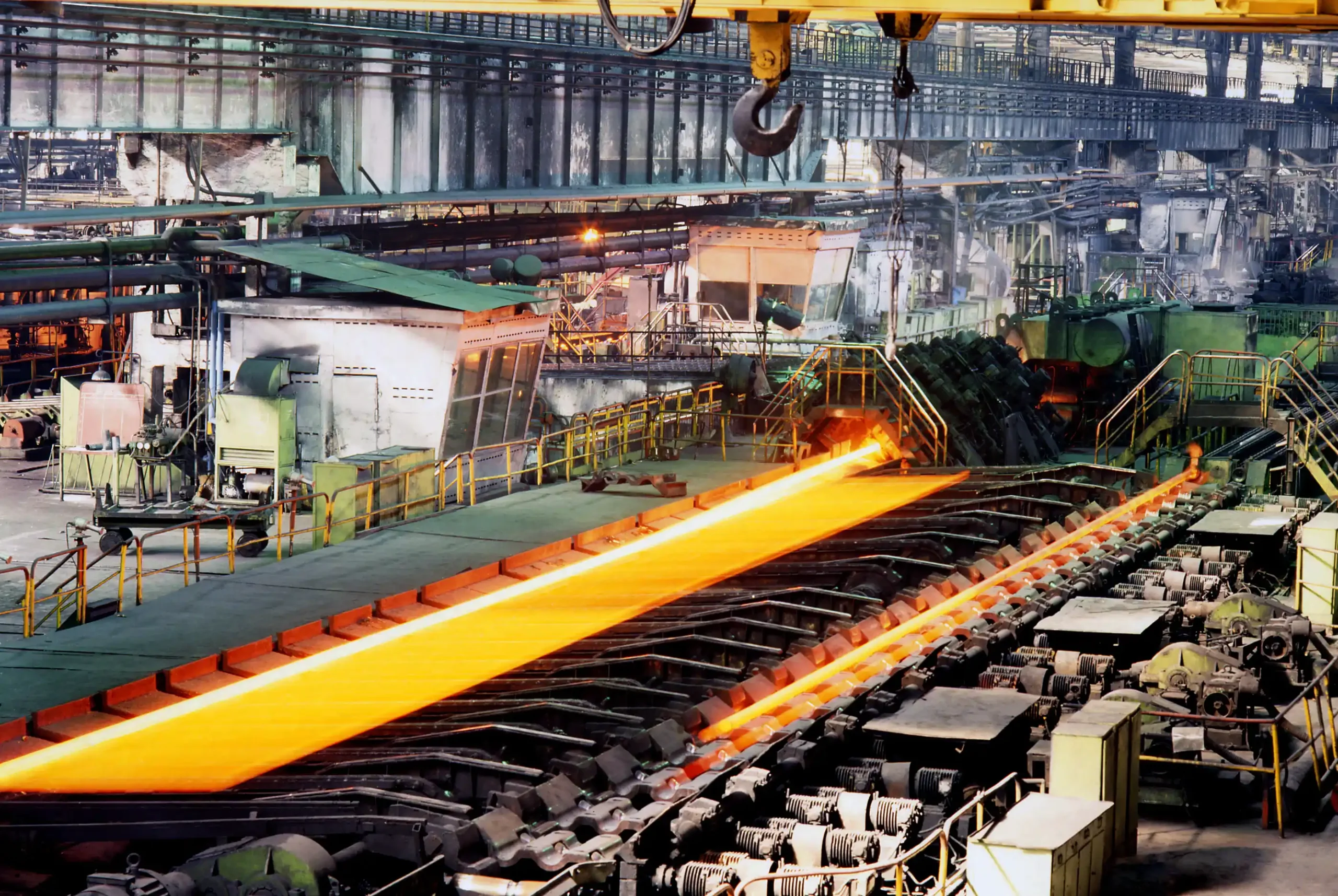
ظهور فناوری نورد در نیمه اول قرن نوزدهم آغاز تولید صنعتی لوله و تیوب را رقم زد. در ابتدا، نوارهای فلزی ورق به کمک تجهیزات قیفی یا غلتک ها به مقاطع دایرهای شکل داده میشدند و سپس با استفاده از فرآیند جوشکاری آهنگری به هم متصل میشدند.
تا اواخر قرن نوزدهم، چندین فرآیند جدید برای تولید تیوب ها و لولههای بدون درز توسعه یافت که منجر به افزایش قابل توجه حجم تولید شد. علیرغم پیشرفتهایی که در فرآیندهای جوشکاری صورت گرفت، بهبودهای مستمر در تکنیکهای تولید لوله بدون درز باعث شد این لولهها بازار را تسخیر کرده و تا زمان جنگ جهانی دوم تقریباً جایگزین لولههای جوش داده شده شوند.
توسعه فرآیند های تولید لوله بدون درز
روش های اصلی تولید لوله های بدون درز در اواخر قرن نوزدهم ظهور کردند. این روش ها با گذشت زمان به فرآیند های تولید با کارایی بالا تکامل یافتهاند:
- فرآیند (Continuous Mandrel Rolling) و فرآیند Push Bench Process: برای لولههایی با قطر خارجی تقریباً 21 تا 178 میلیمتر استفاده میشوند.
- فرآیند Multi-Stand Plug Mill (MPM) : شامل میله ماندرل شناور کنترل شده بوده و در محدوده قطر خارجی حدود 140 تا 406 میلیمتر عمل میکند.
- فرآیند Cross Roll Piercingو Pilger Rolling: مناسب برای تولید لول ههایی با قطر خارجی بین 250 تا 660 میلیمتر.
مراحل فرآیند Mandrel Mill Process
فرآیند میل ماندرل، با یک شمش دایره ای جامد، آغاز میشود که در یک کوره گردان حرارت داده میشود. شمش گرم شده با استفاده از یک سوراخ کن (piercer)، سوراخ میشود تا به یک بدنه توخالی، تبدیل شود. این بدنه توخالی سپس از یک میل ماندرل، عبور داده میشود که قطر خارجی و ضخامت دیواره آن را کاهش میدهد و یک لوله مادر با طول چندگانه شکل میدهد. لوله مادر دوباره گرم شده و با استفاده از یک کاهش دهنده کششی به ابعاد مورد نظر کاهش داده میشود. پس از خنکسازی، لوله بریده، صاف و مراحل تکمیل و بازرسی را طی میکند و سپس برای ارسال آماده میشود.
جزئیات فرآیند میل ماندرل:
- اندازه های لوله: این فرآیند معمولاً برای تولید لولههای کوچکتر بدون درز با قطر 1 تا 6 اینچ (25 تا 150 میلیمتر) استفاده میشود.
- گرمایش و سوراخ کاری (piercer): شمش های فولادی تا دمای 2370 درجه فارنهایت (1300 درجه سانتیگراد) گرم میشوند و سپس سوراخ میشوند.
- نورد ماندرل: یک ماندرل در داخل پوسته توخالی قرار میگیرد و مجموعه از میل ماندرل عبور داده میشود. برخلاف فرآیند میل پلاگ، میل ماندرل ضخامت دیواره را به طور پیوسته با استفاده از مجموعهای از جفت غلتکهای منحنی که در زاویه 90 درجه نسبت به یکدیگر قرار دارند کاهش میدهد.
- کاهش دهنده کششی(Stretch-Reducing Mill): پس از گرم شدن مجدد، قطر لوله برای دستیابی به اندازه نهایی کاهش مییابد.
- مراحل نهایی: لوله به طول مورد نظر بریده، عملیات حرارتی، صاف کاری، بازرسی و آزمایش هیدرو استاتیکی، انجام شده و برای ارسال آماده میشود.
این فرآیند تولید، نمایانگر پیشرفته ترین تکنیک ها در تولید لوله های بدون درز هستند و امکان تولید لوله هایی با کیفیت بالا و ابعاد دقیق را برای کاربرد های متنوع فراهم میکنند.
فرآیند میل پلاگ mill pluge
فرآیند لوله میل پلاگ یک تکنیک ساخت پیشرفته برای تولید لوله های بدون درز، به ویژه لوله هایی با قطر بزرگتر است. این به ویژه برای صنایعی که به لوله های با مقاومت بالا نیاز دارند، مانند نفت و گاز، تولید برق و مهندسی مکانیک مربوط می شود. فرآیند Plug Mill به دلیل دقت در کنترل ابعاد و خواص مکانیکی محصول نهایی لوله شناخته شده است. در زیر کاوش مفصلی از فرآیند لوله میل پلاگ، ارائه شده است.
مراحل فرآیند لوله میل پلاگ
- Preparation of Billets: بیلت ها را در کوره گرم می کنند تا چکش خوار شوند. دمای معمولی گرمایش حدود 1200 تا 1300 درجه سانتیگراد است.
- Piercing: بیلت گرم شده با استفاده از سوراخ کننده چرخشی سوراخ می شود. این پوسته توخالی را تشکیل می دهد که برای تولید لوله ضروری است.
- Insertion of the Plug: بیلت توخالی روی پلاگین سنبه قرار می گیرد. پلاگین در هسته توخالی بیلت وارد می شود و قطر داخلی را در طول فرآیند نورد بعدی کنترل می کند.
- Rolling: شمش، با دوشاخه وارد شده، از یک سری غلتک در میل پلاگین عبور می کند. این فرآیند نورد باعث کاهش قطر خارجی و ضخامت دیواره بیلت می شود.
- Stretch-Reducing:پس از نورد اولیه در میل پلاگین، لوله ممکن است در میل پلاگین، کاهش کشش بیشتر کاهش یابد، که ابعاد لوله را بیشتر اصلاح می کند.
- Cooling and Straightening:لوله تازه تشکیل شده خنک و صاف می شود. در برخی موارد، عملیات حرارتی اضافی برای اطمینان از بهینه بودن خواص مواد انجام می شود.
- Inspection:بازرسی و آزمایش نهایی اطمینان حاصل می کند که لوله تمام مشخصات لازم برای استحکام، دوام و دقت ابعاد را برآورده می کند.
فرآیند میل پلاگ برای تولید seam pipe، با قطر بزرگ تر (140 تا 406 میلیمتر) استفاده میشود. این روش از یک پلاگ برای کنترل ضخامت دیواره در طول نورد استفاده میکند و نتایج با کیفیت بالا برای لولههای با دیواره ضخیمتر ارائه میدهد.
سیستم های بازرسی لوله pipe mill prosecc
کارخانه های مدرن لوله سازی از فناوری های اتوماسیون و دیجیتال برای بهبود کارایی و کیفیت استفاده میکنند. نوآوری ها شامل:
- سیستمهای بازرسی خودکار: استفاده از NDT مبتنی بر هوش مصنوعی برای تشخیص نقص در زمان واقعی.
- کورههای کممصرف: کاهش مصرف انرژی در مرحله گرمایش.
- تکنیکهای پیشرفته جوشکاری: بهبود یکپارچگی درز و کاهش نقص جوش.
فرآیندpipe ball mill process
فرآیند خمش (Pipe Ball Mill) نقشی حیاتی در صنایعی مانند سیمان، معدن، متالورژی و تولید انرژی ایفا میکند. این فرآیند به دلیل کارایی بالا در خرد کردن مواد اولیه به پودرهای ریز، برای کاربرد هایی که به مواد بسیار ریز نیاز دارند، از جمله کلینکر سیمان، سنگ معدن، زغال سنگ و مواد اولیه مختلف دیگر، به طور گستردهای استفاده میشود.
Pipe ball mill چگونه انجام می شود؟
پایپ بال میل، که اغلب به عنوان Tube Mill نیز شناخته میشود، یک دستگاه استوانه ای است که بر اساس برخورد و اصطکاک، برای کاهش اندازه مواد عمل میکند. این ball pipe، شامل یک پوسته استوانه ای چرخان است که با قطعات خرد کننده (معمولاً توپ های فولادی یا سرامیکی) و ماده مورد نظر برای پایپ میل، پر میشود. حرکت مداوم پوسته، عملیات خرد کردن را تضمین میکند، زیرا توپ با مواد و یکدیگر برخورد میکنند.
نکات بنیادی فرآیند pipe ball mill
اصول بنیادی فرآیند pipe ball mill، بر پایه فیزیک و علم مواد بنا شده است، به ویژه:
- نیرو های برخورد: رسانههای خردکننده نیروهای ضربهای به مواد وارد میکنند و آنها را به ذرات کوچکتر میشکنند.
- نیرو های اصطکاکی: چرخش میل پایپ، باعث ایجاد اصطکاک بین رسانههای خردکننده و مواد میشود و اندازه ذرات را بیشتر کاهش میدهد.
- عمل نیروی گریز از مرکز(Centrifugal): با چرخش پوسته، نیروهای گریز از مرکز رسانهها و مواد را بالا میبرند و حرکت آبشاری ایجاد میکنند که کارایی خرد کردن را افزایش میدهد.
اجزای mill prosecc
میل پایپ، لولهای شامل چندین جزء حیاتی است که هر کدام برای بهینه سازی فرآیند خرد کردن طراحی شدهاند:
- Cylindrical Shell: پوسته بیرونی، معمولاً از فولاد ساخته شده، رسانههای خردکننده و ماده مورد نظر برای خرد کردن را در خود جای میدهد. این پوسته با مواد مقاوم در برابر سایش پوشیده شده است تا از فرسایش جلوگیری کند.
- Grinding Media: توپهای فولادی یا سرامیکی برای خرد کردن مواد استفاده میشوند. اندازه و مقدار توپها بر اساس ویژگیهای مواد و میزان ریز بودن مورد نظر تعیین میشوند.
- Inlet and Outlet Trunnions : این اجزا نقاط ورودی و خروجی مواد را فراهم کرده و به عنوان تکیهگاه برای پوسته چرخان عمل میکنند.
- Drive System: معمولاً یک موتور الکتریکی به همراه گیربکس برای تأمین انرژی چرخشی استفاده میشود.
- Separator: در برخی تنظیمات، جداکنندهای برای طبقهبندی مواد نورد شده بر اساس اندازه ذرات استفاده میشود و ذرات بزرگتر را برای پلاگ میل بیشتر بازمیگرداند.
- Feeding and Discharge Mechanism: تغذیه مداوم مواد خام و تخلیه محصول نهایی را تضمین میکند.
کاربردهای فرآیند mill pipe
انعطافپذیری و کارایی میل پلاگ، لوله ای آن را برای صنایع مختلف ضروری کرده است:
تولید سیمان:
- برای خرد کردن کلینکر به پودر ریز سیمان استفاده میشود.
- باعث بهبود ریز بودن و یکنواختی سیمان میشود که برای کیفیت ساخت حیاتی است.
معدن و متالورژی:
- برای خرد کردن سنگ معدنها و آزادسازی مواد معدنی ارزشمند ضروری است.
- در عملیات خرد کردن خشک و مرطوب برای انعطافپذیری حداکثری استفاده میشود.
تولید انرژی:
- برای پودر کردن زغالسنگ به پودر ریز برای استفاده در نیروگاههای حرارتی استفاده میشود.
- کارایی احتراق را افزایش داده و انتشار گازهای گلخانهای را کاهش میدهد.
صنایع شیمیایی و سایر صنایع:
- برای خرد کردن مواد اولیه مورد نیاز برای رنگها، سرامیکها و کودها.
مزایای فرآیند pipe mill
در ادامه به بررسی مزایا و فرآیند میل پایپ پرداخته ایم:
- کارایی: پلاگ میل، با عملیات مداوم و حرکت بهینه رسانههای خردکننده، کارایی بالایی را به دست میآورد.
- انعطافپذیری: برای خرد کردن خشک و مرطوب مناسب است و طیف گستردهای از مواد را پوشش میدهد.
- کنترل اندازه ذرات: سیستمهای پیشرفته امکان کنترل دقیق توزیع اندازه ذرات را فراهم میکنند.
- قابلیت گسترش: پلاگ میل، در اندازههای مختلف موجود هستند و برای عملیات کوچک و بزرگ مناسب هستند.
- بهینه سازی انرژی: pluge mill، مدرن از فناوریهای صرفهجویی در انرژی استفاده میکنند و هزینههای عملیاتی را کاهش میدهند.
نوآوریها در فناوری آسیاب لولهای
پیشرفتهای اخیر در فناوری آسیاب لوله ای عملکرد آن را بیشتر بهبود بخشیده است:
- اتوماسیون: ادغام هوش مصنوعی و اینترنت اشیا برای نظارت و کنترل در زمان واقعی.
- طراحی بهبود یافته لاینر: استفاده از مواد کامپوزیتی پیشرفته برای افزایش طول عمر و کارایی.
- درایوهای سرعت متغیر: امکان تنظیم سرعت چرخش برای شرایط بهینه خرد کردن.
تیم فنی و مهندسی فولاد تبار در تقاطع تخصص و دقت در تلاش است راه حل های بی نظیری را در سیستم های تجاری، مهندسی و صنعتی ارائه دهد. ما در مجموعه فولاد تبار، به دنبال آموزش مطالب علمی در زمینه piping material هستیم تا بتوانیم باعث افزایش مهارت های فنی و مهندسی شما باشیم تعهد ما شما را به اهداف عملیاتی خود تضمین می نماید.
با ما همراه شوید تا عملکرد مهندسی خود را با راه حل های نوآورانه و قابل اعتماد ارتقا دهید
دیدگاهتان را بنویسید