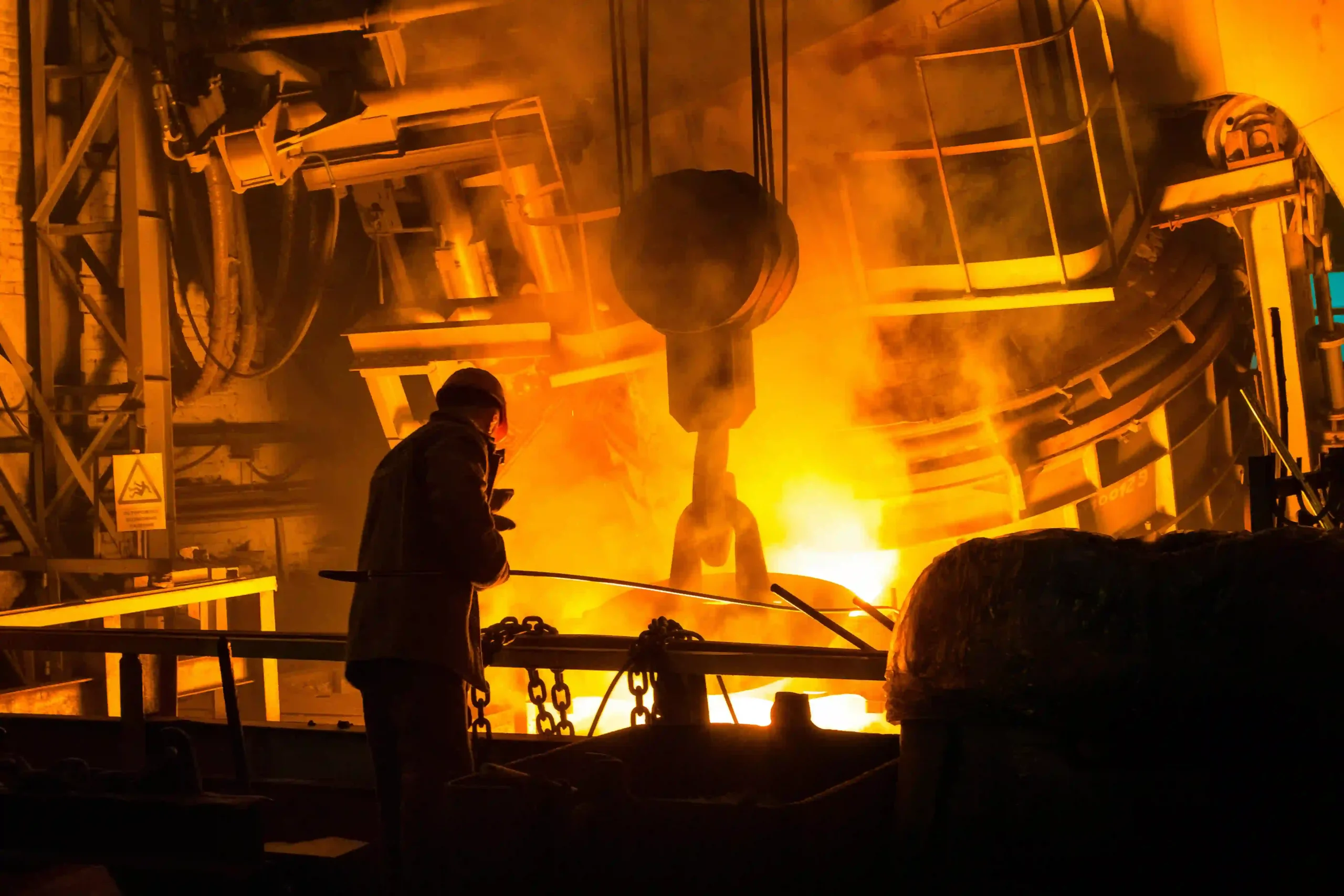
چدن چیست؟
چدن یکی از مواد مهم در دنیای متالورژی و مهندسی است که نقشی اساسی در تولید آلیاژهای فلزی مختلف دارد و در صنایع گوناگون به کار میرود. آهن به عنوان یک فلز عنصری، ستون اصلی بسیاری از ترکیبات آلیاژی مانند فولاد کربنی، فولاد ضد زنگ و سوپرآلیاژها است. با این حال، cast iron در میان این مواد جایگاه ویژهای دارد؛ نه تنها به دلیل اهمیت تاریخیاش، بلکه به خاطر ویژگیها و کاربردهای خاصی که ارائه میدهد. با وجود نامش، چدن اغلب از نظر ترکیب، فرآیندهای تولید و کاربردها اشتباه درک میشود. این مقاله نگاهی جامع به cast iron ارائه میدهد و به تعریف، انواع، روش های تولید و کاربرد های عملی cast iron میپردازد.
Cast iron به خانوادهای از آلیاژهای آهن-کربن اطلاق میشود که حاوی بیش از ۲ درصد کربن هستند. وجود کربن، همراه با مقادیر کمی از سایر عناصر آلیاژی مانند منگنز و سیلیسیم، چدن را از سایر آلیاژ های آهنی مانند فولاد کربنی متمایز میکند. با اینکه نام cast iron نشان دهنده غلظت بالای آهن است، اما به دلیل درصد بالای کربن، میزان آهن موجود در cast iron نسبت به فولاد کربنی کمتر است. عناصر افزوده شده به cast iron خواص مکانیکی آن مانند مقاومت در برابر سایش، سختی و قابلیت ماشینکاری را بهبود میبخشند.
انواع cast iron
چدن یک ماده یکپارچه نیست، بلکه شامل انواع مختلفی است که هر کدام ویژگی های خاصی بر اساس ترکیب و ریزساختار خود دارند. انواع اصلی cast iron عبارتند از:
- Ductile cast iron (نشکن): که به چدن گرهای نیز معروف است، حاوی گرافیت به شکل گرههای کروی کوچک است. شکل کروی گرافیت باعث میشود این نوع چدن انعطافپذیرتر و مقاومتر در برابر ترکخوردگی باشد و در مقایسه با سایر cast iron استحکام و toughness بالاتری داشته باشد.
- :Grey cast iron رایجترین نوع چدن است و دارای گرافیت به شکل پولکهایی است که به سطح شکست آن ظاهر خاکستری میدهد. این پولکها قابلیت ماشینکاری آن را افزایش میدهند، اما مقاومت کششی آن را کاهش داده و آن را شکنندهتر میکنند. چدن خاکستری به دلیل خاصیت جذب ارتعاشات بسیار شناخته شده است.
- :White cast iron در این نوع چدن، کربن به جای گرافیت به صورت کاربید آهن وجود دارد. این امر باعث ایجاد مادهای سخت و شکننده با مقاومت بالا در برابر سایش میشود. چدن سفید در کاربردهایی که مقاومت به سایش اهمیت دارد استفاده میشود، اما به دلیل شکنندگی برای کاربردهای سازهای محدود است.
- :Malleable cast iron این نوع چدن با عملیات حرارتی چدن سفید، تولید میشود که کاربید آهن آن به گرههای گرافیت تبدیل میشود. این فرآیند انعطافپذیری و toughness ماده را بهبود میبخشد و آن را به چدن داکتیل نزدیک میکند. چدن چکش خوار، در کاربردهایی که نیاز به استحکام و انعطاف وجود دارد، استفاده میشود.
دسته بندی آلیاژ های چدن
آلیاژ های cast iron معمولاً شامل عناصر زیر هستند:
- آهن: (Fe) عنصر اصلی که پایه آلیاژ را تشکیل میدهد.
- کربن : (C)در محدوده ۲ تا ۴ درصد که مشخصه اصلی چدن است.
- سیلیسیم: (Si) به میزان ۱ تا ۳ درصد برای تسهیل تشکیل گرافیت و بهبود سیالیت افزوده میشود.
- منگنز: (Mn) سختی و استحکام را افزایش داده و اثر شکنندگی ناشی از گوگرد را خنثی میکند.
- عناصر دیگر: مقادیر کمی گوگرد و فسفر ممکن است وجود داشته باشد که میتوانند شکنندگی را تحت تأثیر قرار دهند، اما معمولاً برای دستیابی به خواص مکانیکی مطلوب کنترل میشوند.
چدن چگونه تولید میشود؟
فرآیند تولید cast iron، عامل کلیدی است که بر ویژگیها و کاربردهای آن تأثیر میگذارد. نام “چدن” از تکنیک تولید آن گرفته شده است. فرآیند تولید با استخراج آهن از سنگ آهن آغاز میشود، سپس با پالایش و افزودن عناصر آلیاژی به ترکیب مورد نظر میرسد.
- ذوب سنگ آهن: سنگ آهن در کوره ذوب میشود تا آهن مذاب استخراج شود. این فرآیند با استفاده از کک به عنوان عامل احیا و مواد گدازآور برای حذف ناخالصیها انجام میشود. آهن مذاب حاصل دارای سطوح بالایی از کربن و عناصر دیگر است.
- ریختهگری شمشها: آهن مذاب در قالبها ریخته میشود تا شمشها تشکیل شوند. این شمشها به عنوان ماده اولیه برای فرآوریهای بعدی استفاده میشوند.
- ذوب مجدد و افزودن آلیاژها: شمشهای چدن دوباره ذوب شده و عناصر آلیاژی مانند منگنز، سیلیکون و گاهی اوقات کروم یا نیکل برای تغییر ویژگیهای محصول نهایی اضافه میشوند. فرآیندهای حرارتی نیز ممکن است برای دستیابی به ویژگیهای خاص اعمال شوند.
اصطلاح “Cast” از فرآیند ریخته گری آن گرفته شده است. مراحل تولید چدن به شرح زیر است:
- ذوب سنگ آهن: فرآیند با گرم کردن سنگ آهن در کوره تا حالت مذاب شدن آغاز میشود. کربن به صورت کک اضافه میشود تا مقدار کربن به سطح مطلوب برسد.
- آلیاژ سازی: در طول فرآیند ذوب، عناصر آلیاژی مانند سیلیسیم و منگنز به منظور تغییر خواص مکانیکی به مذاب اضافه میشوند.
- ریخته گری: پس از رسیدن به ترکیب مورد نظر، فلز مذاب در قالبها ریخته شده و اجازه داده میشود تا خنک و جامد شود. این قالبها میتوانند به شکل شمش یا قطعات نهایی باشند.
- ذوب مجدد و :Heat-treatmentدر برخی موارد، چدن مجدداً ذوب شده و به اشکال خاصی ریخته گری میشود و ممکن است عملیات حرارتی برای دستیابی به ریز ساختار مورد نظر انجام شود. به عنوان مثال، چدن سفید برای تبدیل به چدن چکش خوار عملیات حرارتی میشود.
cast iron به دلیل نقطه ذوب پایین و سیالیت عالی برای ریختهگری اشکال پیچیده و مقاطع نازک بسیار مناسب است.
ویژگی های Cast iron
- سختی و مقاومت در برابر سایش بالا: محتوای بالای کربن و وجود کاربید آهن، سختی فوقالعادهای به چدن میبخشد.
- شکنندگی: اکثر انواع چدن، بهویژه چدن سفید، شکننده هستند و تحت کشش میشکنند.
- سیالیت خوب: چدن بهراحتی در حالت مذاب جریان پیدا میکند و امکان ریختهگری اشکال پیچیده را فراهم میسازد.
- جذب ارتعاشات: ساختار پولکی گرافیت در چدن خاکستری ارتعاشات و صدا را جذب میکند.
- مقاومت در برابر تغییر شکل: چدن در برابر بارهای فشاری به خوبی شکل خود را حفظ میکند و کمتر دچار تغییر شکل میشود.
کاربردهای cast iron
چدن از گذشته تاکنون در کاربرد های متنوعی استفاده شده و بسیاری از این کاربردها همچنان ادامه دارند. هر نوع چدن بر اساس ویژگی های خود در کاربرد های خاصی استفاده میشود:
-
- Ductile cast iron در قطعاتی که نیاز به استحکام و toughness دارند مانند بلوک موتور، لوله ها و cranck shaft استفاده میشود.
- Grey cast iron به دلیل قابلیت ماشین کاری و جذب ارتعاش در دیسک های ترمز، بستر ماشینآلات، پوسته پمپ استفاده میشود.
- White cast iron برای سطوح مقاوم به سایش مانند لاینر آسیاب ها، پوسته پمپ های دوغاب و تجهیزات معدنی استفاده میشود.
- Malleable cast iron در قطعات خودرو، ماشین آلات کشاورزی و اتصالات به دلیل انعطافپذیری و استحکام بالا استفاده میشود.
محدودیت های استفاده از cast iron
با وجود مزایای آن، چدن محدودیتهایی نیز دارد:
- شکنندگی: بیشتر انواع cast iron تحت فشار کشش میشکنند.
- حساسیت به خوردگی: cast iron در صورت عدم نگهداری مناسب در طول زمان دچار خوردگی میشود.
- وزن زیاد: قطعات cast iron معمولاً سنگین تر از قطعات ساخت هشده از مواد جایگزین مانند آلومینیوم یا کامپوزیت ها هستند.
تیم فنی و مهندسی فولاد تبار در تقاطع تخصص و دقت در تلاش است راه حل های بی نظیری را در سیستم های تجاری، مهندسی و صنعتی ارائه دهد. ما در مجموعه فولاد تبار، به دنبال آموزش مطالب علمی در زمینه piping material هستیم تا بتوانیم باعث افزایش مهارت های فنی و مهندسی شما باشیم تعهد ما شما را به اهداف عملیاتی خود تضمین می نماید.
با ما همراه شوید تا عملکرد مهندسی خود را با راه حل های نوآورانه و قابل اعتماد ارتقا دهید
دیدگاهتان را بنویسید